New solutions for your applications
High-performance fiber-reinforced composites for aerospace applications
The aerospace industry is evolving rapidly, demanding materials that remain reliable and high-performing under extreme conditions – while maintaining a low weight. The requirements in space applications are equally demanding: materials must withstand both mechanical stress and thermal extremes. This is exactly where Schunk’s fiber-reinforced composites demonstrate their full potential. Our solutions with polymer, carbon or ceramic matrices enable advanced lightweight designs and make a key contribution to improving efficiency and safety in aerospace applications. A prime example: our sealing rings used in engine components. They combine ultra-low weight with outstanding fatigue strength – properties that are not achievable with conventional materials.
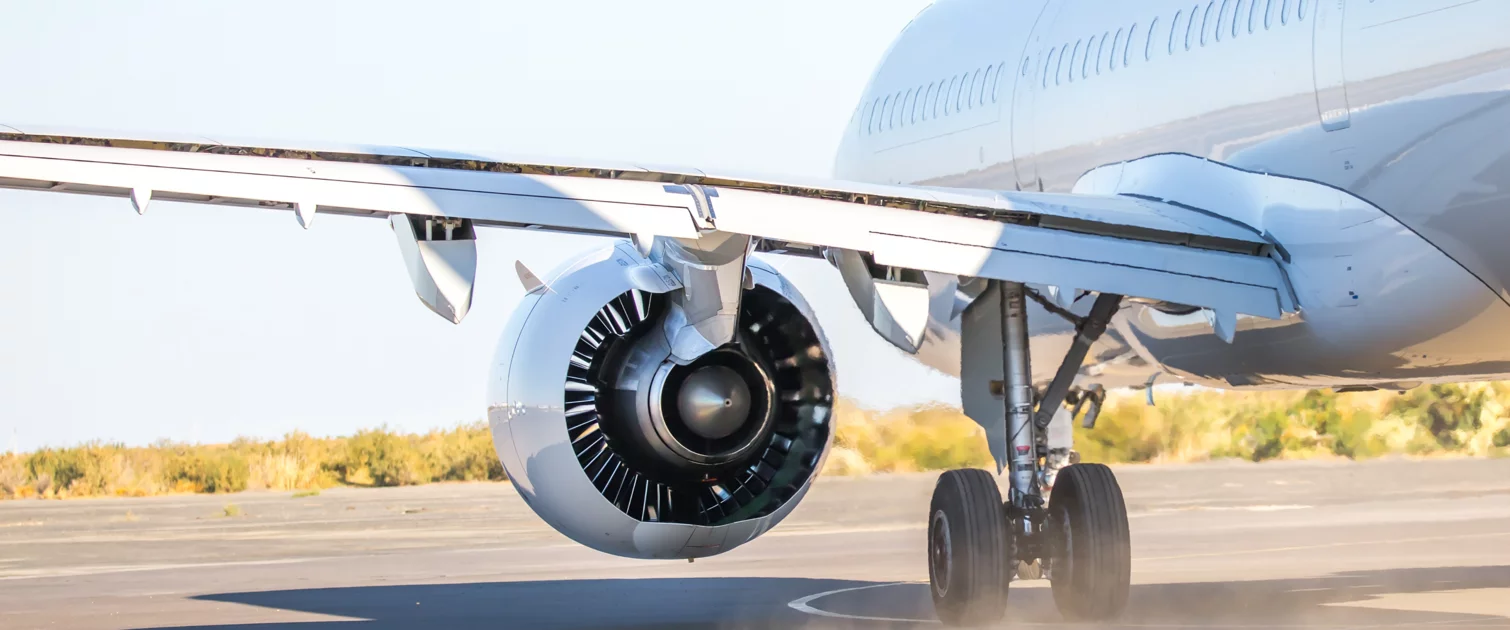
Manufacturing expertise for aerospace applications
Schunk is your experienced partner for high-end composite solutions in aerospace. Our production sites are tailored to the stringent requirements of leading international engine manufacturers. By tightly integrating material development, manufacturing technology, and quality assurance, we ensure maximum precision and process reliability. With our comprehensive engineering expertise, we develop components that convince both technologically and economically.
Your benefits with Schunk high-performance composites
-
Maximum strength and stiffness at minimal
-
Excellent resistance to temperature and media
-
Material solutions for ultra-lightweight and high-load requirements
-
Tailor-made composite components and manufacturing processes
-
Reliability for safety-critical applications
Tailor-made high-performance composites for extreme conditions
Requirements for materials in aerospace continue to rise – solutions are needed that remain reliable, thermally stable, and weight-optimized under extreme conditions. With our fiber-reinforced composites – including Oxide Fiber Composites (OFC) – we offer exactly that: high-performance materials known for their versatility in processing and outstanding performance.
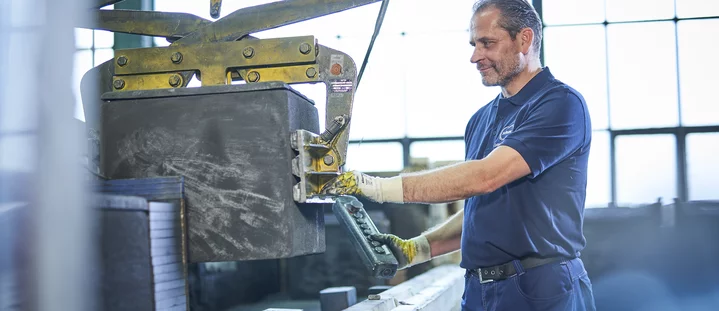
Advanced materials technology
Our composites impress with high-temperature-stable performance fibers such as aluminum oxide (Al₂O₃), mullite, or YAG. Thanks to water-based colloidal processing, we manufacture components with excellent dimensional stability and low porosity – even at application temperatures of up to 1,300 °C.
Additional material characteristics:
-
Excellent thermal shock resistance
-
Electrical insulation and magnetic shielding
-
Adjustable emission and absorption coefficients
-
No fiber coating required for WMC variants
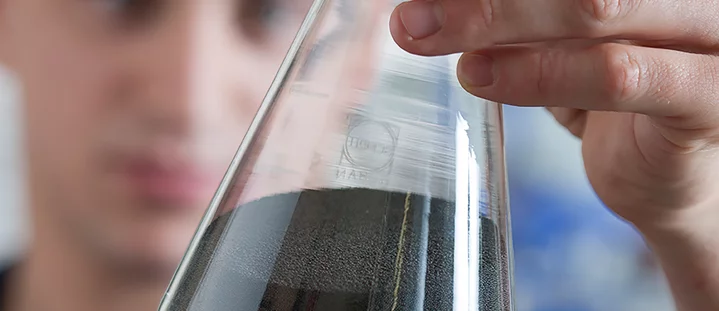
Precision manufacturing for small and large components
Our production facilities are designed to handle both large-format and high-precision components. With CNC-controlled milling and turning centers, robotic handling, and advanced waterjet technology, we produce components up to 3.1 × 2.0 × Ø 1.6 m³ – available in single-unit or series production.
Development partner with vision
As a seasoned partner, Schunk covers the entire value chain – from material development and simulation to process design and quality assurance. Our core competencies:
-
In-house simulation and development expertise
-
Willingness to invest in customer-specific requirements
-
Advanced metrology for consistent high quality
-
Flexible production volumes – from prototypes to large-scale series
Material diversity and technologies for composite components
Our materials expertise includes a broad portfolio of fiber-reinforced plastics such as CFRP (carbon fiber-reinforced polymer), GFRP (glass fiber-reinforced polymer), and AFRP, as well as ceramic matrix composites such as CFC, C/SiC, OFC, or SiC/SiC. For demanding applications, we also implement hybrid material concepts in multi-material lightweight construction.
We support you throughout the entire development process – from simulation, material selection, and initial prototypes to full-scale production. We use state-of-the-art methods such as autoclave technology, wet pressing, and cost-efficient mass production techniques like filament winding. Our portfolio also includes SMC (Sheet Molding Compound), RTM (Resin Transfer Molding), and vacuum infusion processes.
Applications in safety-critical environments
Our materials and components are used wherever extreme reliability is required. This includes tribologically stressed bearings, pistons, seals, and sliders, as well as structural parts in ultra-lightweight construction. Our expertise also plays a vital role in the thermal treatment of engine components such as turbine blades.
Quality and responsibility for your projects
With Schunk, you choose a technology partner that combines innovation with consistent customer focus. Our safety culture is deeply rooted in our company – all employees involved in safety-relevant components are regularly trained and sensitized. The result: reliable, repeatable quality at the highest level.

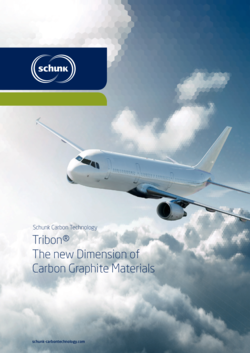
The new Dimension of
Carbon Graphite Materials
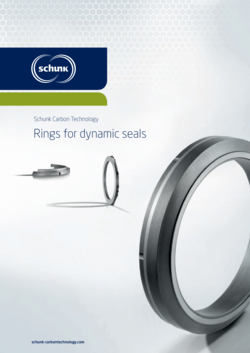
Carbon Materials in Dynamic Seals
Downloads
Let us advise you
Feel free to contact us if you have any questions about our services for the aerospace industry.